Waste in lean manufacturing and how to reduce it
It wasn’t so long ago that the idea of lean manufacturing was the preserve of high-tech, forward-thinking factories in Japan. But in an age where manufacturers, all over the world, leave no stone unturned in their quest for efficiency and profitability, lean manufacturing has become far more commonplace.
The enemy of lean manufacturing, however, is waste. It can be caused by a variety of things, and can have a major effect on balance sheets, delivery deadlines and customer satisfaction, alike. In this guide, we’ll explore the main causes of waste in lean manufacturing, and how Mitie can help you deal with them when they occur.
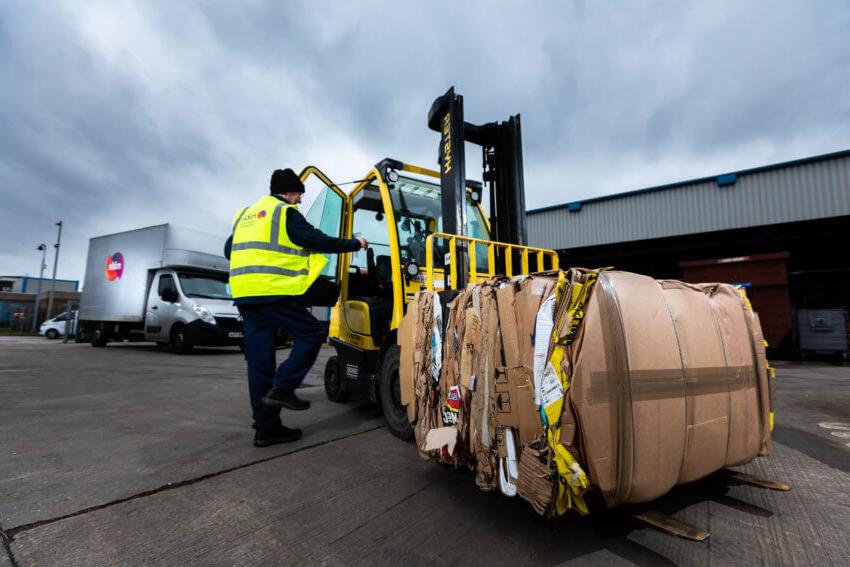
What is lean manufacturing and lean manufacturing waste?
It’s easy to think of waste as physical material that is thrown into the bin, but in a manufacturing context, the meaning is much wider. Specifically, it refers to any effort or expenditure that doesn’t contribute to the creation of a product that is ultimately bought by a customer.
A business that can eliminate waste at every stage of its production process – from raw materials to the point of sale – is maximising its efficiency, profitability and environmental friendliness.
Sustainability is a priority at Mitie. Our waste management specialists work closely with customers to help them reduce waste and improve operational and labour efficiencies. And by working with their procurement teams, we make sure that resources become part of the circular economy rather than going to landfill.
Using our approach to waste management, we helped a major aerospace customer to identify areas where manufacturing waste could be reduced and efficiencies made. We conducted a ‘cradle-to-grave’ waste mapping exercise across their 10 key UK sites and, as a result, over 3 years they saved £1.6m on waste management costs.

What are the key wastes in lean manufacturing?
Waste in lean manufacturing can come from many different sources, and here are some common areas that affect companies across the manufacturing sector:
Transport
This doesn’t necessarily have to be related to the transport of materials or goods from site to site. However, poor logistical planning, or trucks that run below capacity, do generate fuel-related waste. Transport can also be a generator of waste within individual sites and factories. For example, if adjacent parts of a manufacturing process are located at opposite ends of a factory, more energy is used to move items further. This also increases wear and tear on the vehicles used for the transport and generates higher labour costs as more staff are needed to operate the vehicles.
Inventory
When materials or goods are stored for longer than is necessary, extra costs are generated due to the space and facilities needed to store them. There are many causes of excessive inventory, such as overproduction, delays at points within the production process, or excessive transportation where processes aren’t as efficient as they could be. The knock-on impact of poor inventory management can be seen directly in cash flow, balance sheet metrics and, in a worst case, obsolete goods.
Motion
Anything that is moving has a cost attached to it, whether that’s mechanical movement in a vehicle, on a conveyor belt, or human movement of employees lifting and carrying items. This means that any movement that isn’t kept to the lowest possible level counts as waste. This can be caused by poor building layouts, badly designed processes, unconnected systems and siloed operations that lack integration.
Waiting
The old adage ‘time is money’ is especially true in manufacturing. Anything that waits around – goods, equipment, people – is burning through cash while not doing anything productive. And this waste can easily escalate. If production processes are rushed to make up for lost time, mistakes can be made, corners can get cut, and defects creep in that render goods unsaleable. Bad process control, poor communications, unplanned downtime and issues in the supply chain can all cause waiting-related waste.

Overproduction
This doesn’t mean making too many goods: it refers to one stage of a production process completing the task before the next stage is ready to start. This leads to unnecessary logjams at certain points in the process, slows down the overall speed of production and increases storage needs. Unreliable processes, poor just-in-time supplier management, wrong forecasting and a lack of clarity in production schedules or customer expectations, can all generate waste in this case.
Over-processing
Over-processing is where there are certain elements of a production process that simply don’t need to be there. Obviously, these additional tasks tend to be part of the overall process, like paperwork, rather than in the actual product manufacture. Not mapping processes out correctly, misunderstanding what customers want, and miscommunication or human error, can all contribute to over-processing.
Defects
There are many risks of defects within the manufacturing processes. For example, mistakes in manufacture, errors in quality control, unnecessary inventory fluctuations, poor design, and badly planned workflows. Defects take time and money to fix, which can quickly have an impact on the smooth running of other areas, including customer satisfaction, reputational damage, and ultimately, demand for the product.
Three simple steps to start reducing your waste
Whichever type of waste your business is struggling with, there is a simple three-step process that can help you discover the right way to reduce or eliminate it:
- Identify and assess
Conduct a thorough audit into the source of the waste and any processes and activities connected to it. This should help you work out whether there is anything unnecessary that you can get rid of. - Remove and improve
As you take out what you don’t need, look for ways to improve and optimise the things that are necessary. - Repeat
Keep reviewing the adjusted processes, to minimise waste and keep manufacturing running as lean and efficiently as possible.

Get support for your lean manufacturing waste management with Mitie
Mitie takes a ‘resource not waste’ approach which prioritises waste avoidance and minimisation through a sustainability led ‘prevent, reduce, reuse, and recycle’ approach:
- Prevent
Target the unnecessary consumption of goods and services. Consider the supply chain and, where possible, reduce the volume, mass, or toxicity. - Reduce
If waste can’t be prevented, we look at how it can be reduced in the process. For example, by using fewer virgin materials, reducing energy consumption, or reducing its toxicity. - Reuse
Find ways to reuse materials internally or across sites. Examining the role of packaging and modifying to enable less use, without impacting performance. Exploring cost-effective, ethical, and environmental disposal routes where necessary from our own resource platform, Waste Match. - Recycle
If we can’t help you prevent, reduce or reuse waste, we’ll help you find the best way to recycle. Recycling can result in materials that are more energy-efficient, less polluting and more cost-effective to produce, while avoiding the consumption of virgin materials. Legislative compliance, eco-credentials and over 30 years of experience mean that we typically achieve more than 90% recycle rates within 12 months.
Using our approach, coupled with the above waste management techniques, Mitie is delivering on the promise to help lean manufacturing drive out inefficiency and make cost and sustainability savings.
Contact the team to discover more about how Mitie can help your business reduce your waste in lean manufacturing.
Read next
Mitie saves 80 tonnes of uniform from landfill with recycling project
Mitie saves 80 tonnes of uniform from landfill with innovative recycling project

What is the link between FM and sustainability?
Pradyumna V. Pandit, MD of Sustainability and Energy Services at Mitie gives his insight on the link between FM and sustainability. “As a sector that is often working behind the scenes, World FM Day…

Mitie wins triple gold in the Green Impact competition
Our Mitie Communities colleagues has won three awards in this year’s NUS Green Impact competition for contributing to sustainability at University College London Hospital (UCLH). What is Green Impact? Green Impact is a United Nations award-winning programme designed to…